Basic Info.
Model NO.
JSD53B
Assembly Structure
Integral Type Extruder
Screw
Twin-Screw
Engagement System
Full Intermeshing
Screw Channel Structure
Deep Screw
Exhaust
Exhaust
Automation
Automatic
Computerized
Computerized
Material Handled
PE, PP, ABS, PVC, EPS, PA6, PA66
Certificate
CE, ISO, SGS
Production Quantity
1000sets/Year
Machine Tools
CNC Center
Color
Beautiful
Transport Package
Wooden Boxes
Specification
JSD26
Trademark
JSD
Origin
China
HS Code
84772010
Production Capacity
200sets/Year
Product Description
The extruder structure adopes building block design, The extruder is made of building block system, and the screw element and the shaft are connected by an involute spline;
Threaded element material: high speed tool steel (W6Mo5Cr4V2), vacuum quenched;
Screw rotation direction: co-rotating;
The barrel adopts modular design;
Natural ventilation ventilation port ventilation port
1 2 3 4 5 6 7 8 9 10
Barrel structure: Section 1 is the main feeding port, Section 5 is the natural ventilation port, Section 7 is the natural ventilation port, Section 9 is the natural ventilation t port, and the other 6 barrels are closed barrels.
Barrel material: bi-metal wear-resistant bushing (alpha- 101 alloy);
Barrel cooling: soft water cooling is adopted. The main inlet and return pipes of cooling water are made of stainless steel, and the inlet regulating valves of each barrel are made of stainless steel; Motor power of water pump of soft water circulating cooling system is 0.75kw;
Cover material: stainless steel
Barrel heating: electric heating, about 50KW; Section 1 to 9 are cast iron. The screen changing head is a copper heater
Process flow:
Dryer tower→Screw feeder → Force feeder→ Parallel twin screw extruder →Hydraulic filer exchanger→ Mould head →water cooling tank →Plastic standard cutter→ Finished product packing.
Detailed description of each item:
1.Screw Feeder : conveyor pet flakes into the main machine.
2.Force feeder: feed the material to the extruder with a designed speed, the speed can be adjusted.
3.Parallel twin screw extruder: plasticizing material and exhausting gas.
4.High-speed Net exchanging system and Die-head: filter material impurity, to make production more stable.
5.Water tank: cooling the PET noodles.
6. Under water cutting : cut the PET noodles into granuels.
7. Vibrator: screen standard granueles after cutting
8.Air conveyor and Storage Silo: fan conveyor , storage the silo with big jumbo bags
9.Electrical control box: control machine working and stop
Threaded element material: high speed tool steel (W6Mo5Cr4V2), vacuum quenched;
Screw rotation direction: co-rotating;
The barrel adopts modular design;
Natural ventilation ventilation port ventilation port
1 2 3 4 5 6 7 8 9 10
Barrel structure: Section 1 is the main feeding port, Section 5 is the natural ventilation port, Section 7 is the natural ventilation port, Section 9 is the natural ventilation t port, and the other 6 barrels are closed barrels.
Barrel material: bi-metal wear-resistant bushing (alpha- 101 alloy);
Barrel cooling: soft water cooling is adopted. The main inlet and return pipes of cooling water are made of stainless steel, and the inlet regulating valves of each barrel are made of stainless steel; Motor power of water pump of soft water circulating cooling system is 0.75kw;
Cover material: stainless steel
Barrel heating: electric heating, about 50KW; Section 1 to 9 are cast iron. The screen changing head is a copper heater
Process flow:
Dryer tower→Screw feeder → Force feeder→ Parallel twin screw extruder →Hydraulic filer exchanger→ Mould head →water cooling tank →Plastic standard cutter→ Finished product packing.
Detailed description of each item:
1.Screw Feeder : conveyor pet flakes into the main machine.
2.Force feeder: feed the material to the extruder with a designed speed, the speed can be adjusted.
3.Parallel twin screw extruder: plasticizing material and exhausting gas.
4.High-speed Net exchanging system and Die-head: filter material impurity, to make production more stable.
5.Water tank: cooling the PET noodles.
6. Under water cutting : cut the PET noodles into granuels.
7. Vibrator: screen standard granueles after cutting
8.Air conveyor and Storage Silo: fan conveyor , storage the silo with big jumbo bags
9.Electrical control box: control machine working and stop
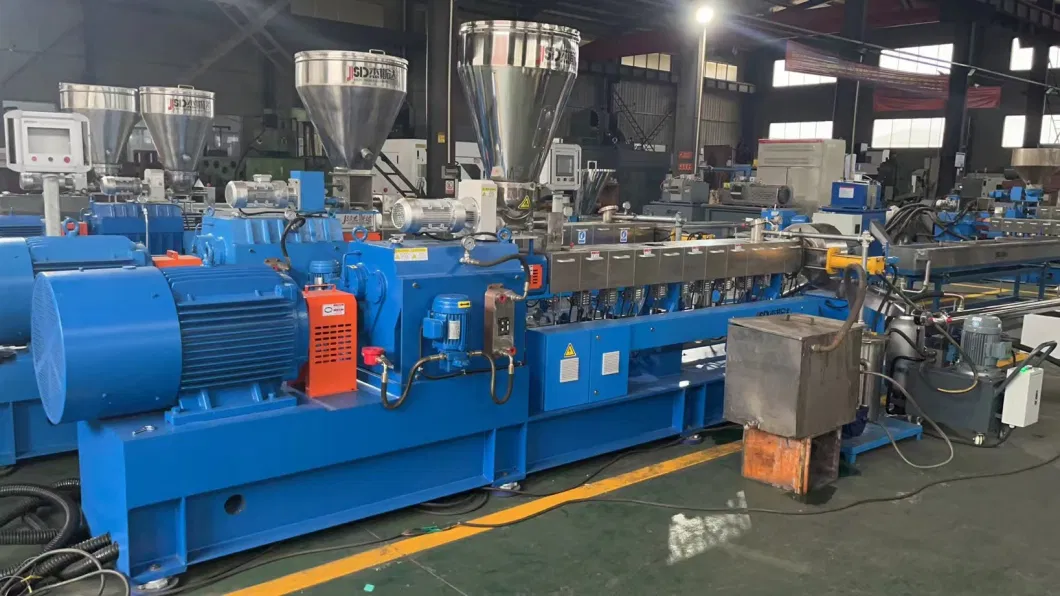
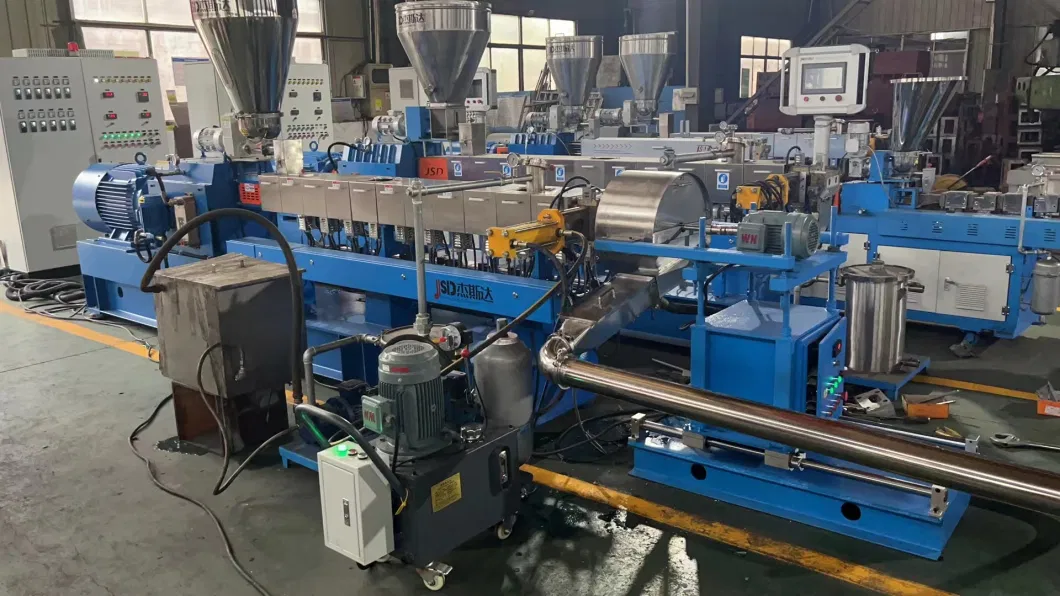