- Overview
- Product Description
- Product Parameters
- Application
- Our Domestic Partners
- Certifications
- Our Advantages
- FAQ
Basic Info.
Product Description
Our factory offers a vast range of Color Masterbatch ranging from light to dark colors, transparent to apaque colors and normal to specialty colors.
Do you know what is color masterbatch? what is color masterbatch composed of ?
Color masterbatch, as it's name shows, is used to color something. In plastic industry, we use color masterbatch to color plastics products. Before the color masterbatch is invented, industry used to color plastics with pigments (which is powder-like and does harm to workers). So color masterbatch is a good plastic-colorant solution, some of our cutomers are starting to trying it these years while it was invented last decade. They give color masterbbatch a very good feedback.
The most important benefit of Masterbatches over a powdered pigment is that masterbatches are carefully designed to create optimal dispersion in a polymer pattern. Besides it, color masterbatches are cost-effective, good on long productions runs, and others.
The masterbatches provide essential properties like UV stability, flame retardancy, anti oxidants, colour, jetness, etc. So there are various masterbatches like White Masterbatch, Black Masterbatch, Additive Masterbatch, Colour Masterbatch and Special Effect Masterbatch that our Chongyuan Fine Chemical are manufacturing. We offer best quality and competitive price.
*For specific color masterbatch, send an inqury to me, I will send you our catalogue.
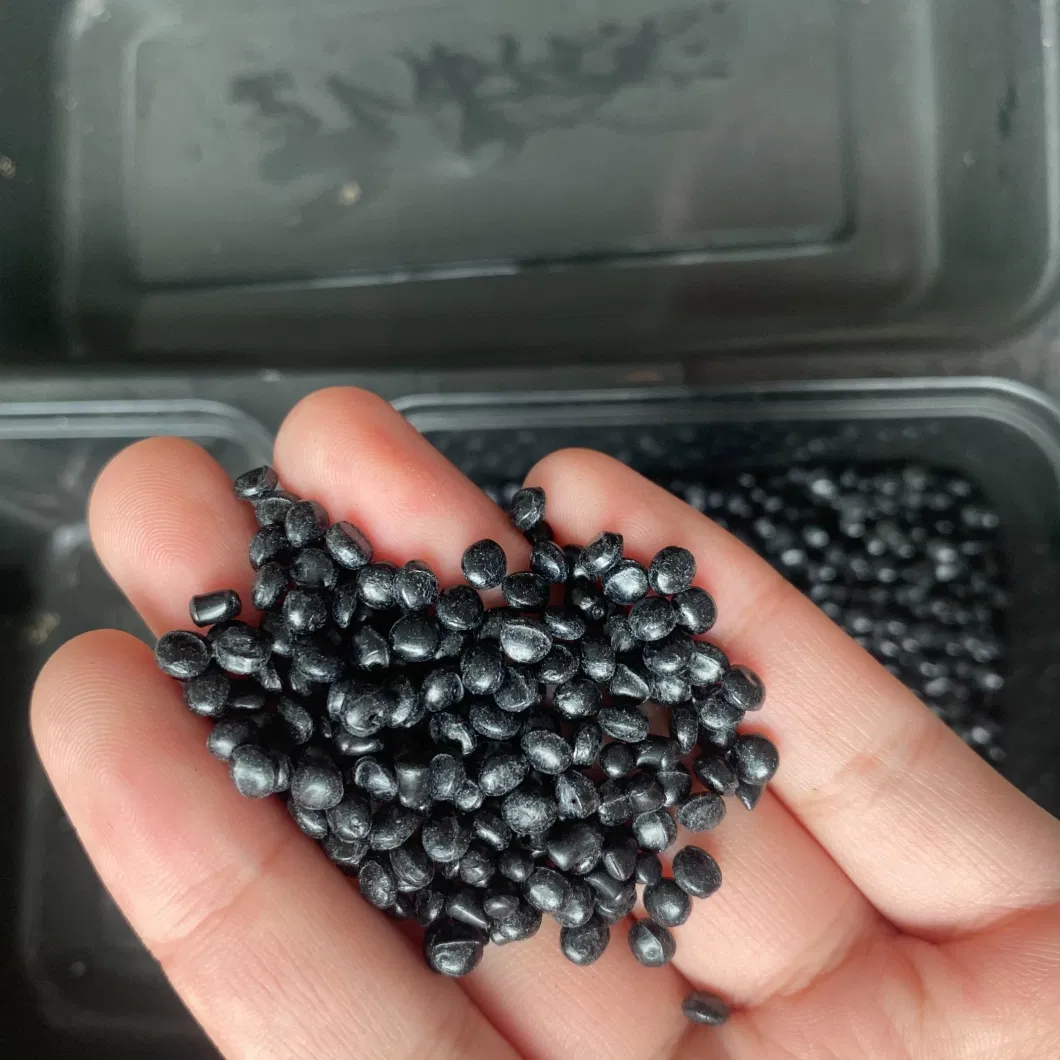
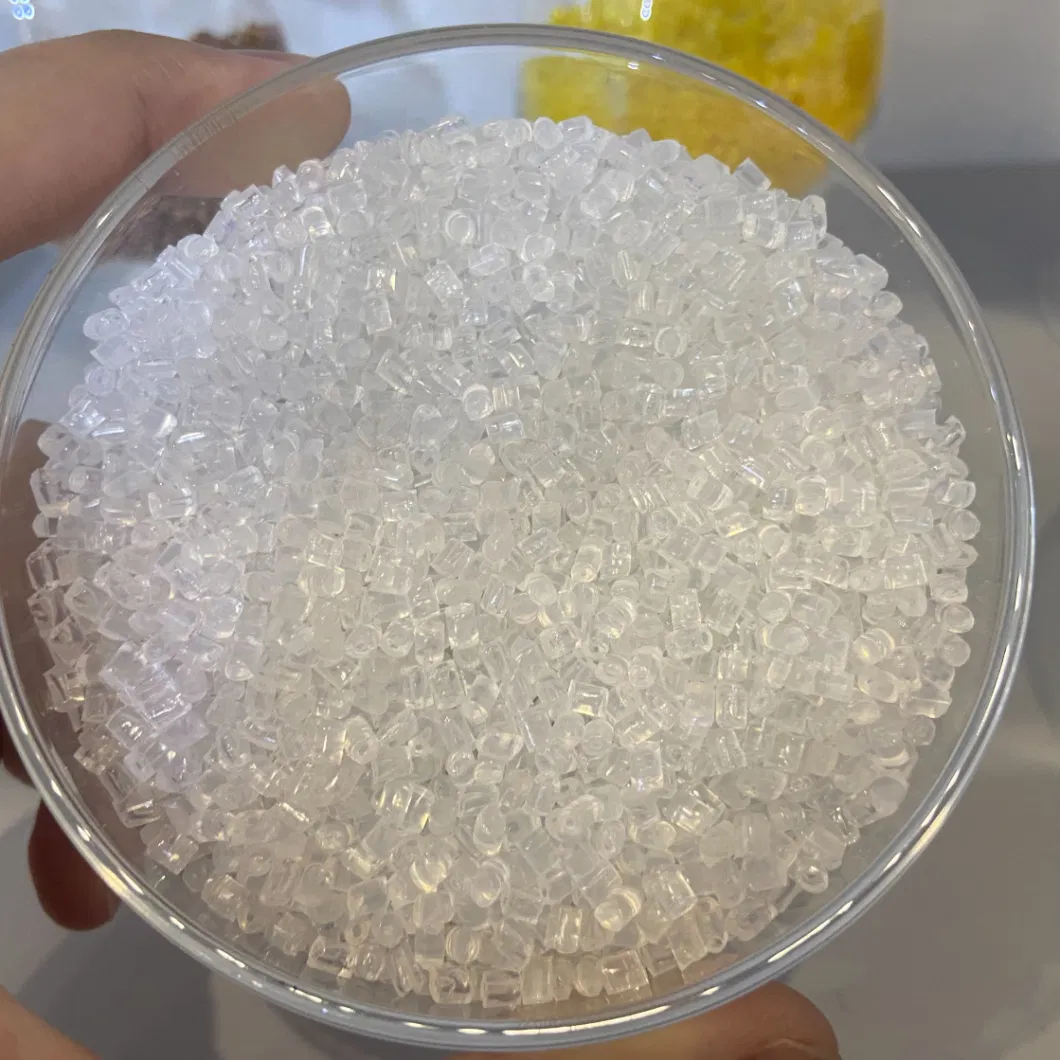
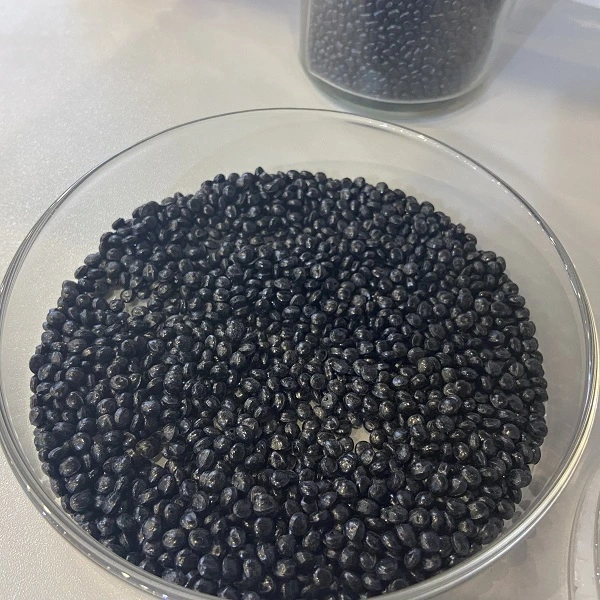
Product Parameters | |||
Melt Flow Index (MFI) | > 5 (g/10min) | Light resistance | 5~8 |
Processing temperature | 150~300°C | Weather resistance | 4~5 |
Moisture content | <0.2% | Delta E (△E) | ≤0.8 |
Transference resistance | 4~5 | ||
Processing conditions | |||
Drying Cond | 110-125°C * 12h | Molding Temp | 80-150°C |
Injection Temp. | 300-330 | Injection Speed | Low to Medium |
Moisture Control | <0.2% |
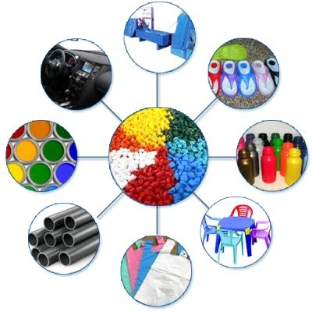
Packaging Materials
Daily Necessities
Home Appliances
Building Materials
Sanitary Supplies
Photovoltaic Applications
New Energy Sector
Toys and more
Filler Masterbatch, for example
1. PET MASTERBATCH (Application in packaging bottles, food packaging, materials, accessories.
2. PP Nonwoven Masterbatch (Application in recycled plastic
3. PP Woven Masterbatch
4. ABS Masterbatch (Used in a wide variety of commerical and industrial applications, now automobiles, eletrical equipment, sports equipment, toys, construction
...
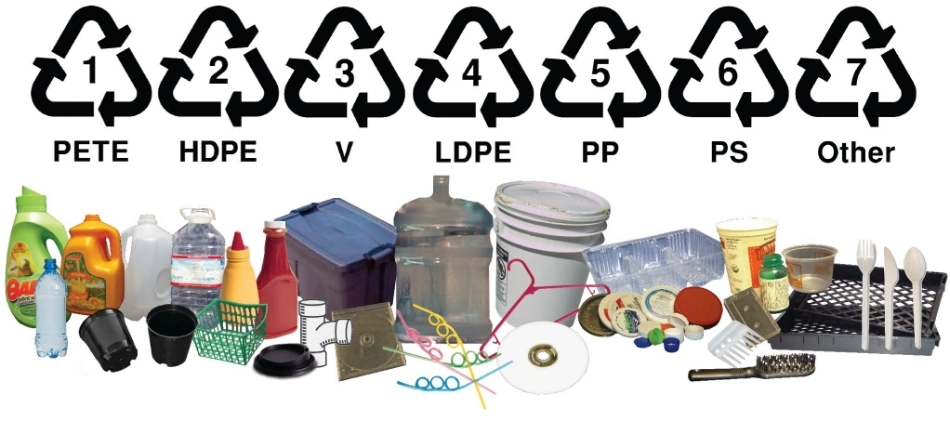
Those are some of our domestic partners, and we take pride in serving them with excellence.
- Auto industry: Red Fairy (leading supplier to BYD and CATL)
- Food Packaging: Wahaha, JUNLEBAO, ARROW, MENNIU, YILI, KFC
- Home appliance: Media, GREE, ECOVACS, HISENSE
- Building: RIFENG, JINNIU, GAO, VASEN
RoHS/REACH/PAHs/DINP
America FDA 177.1520
China GB 4806.6-2016 GB 9685-2016
Europe (EC) No1935/2004 (EU) No10/2011
......
*Note: no bisphenol A, plasticizer and other qualified substances
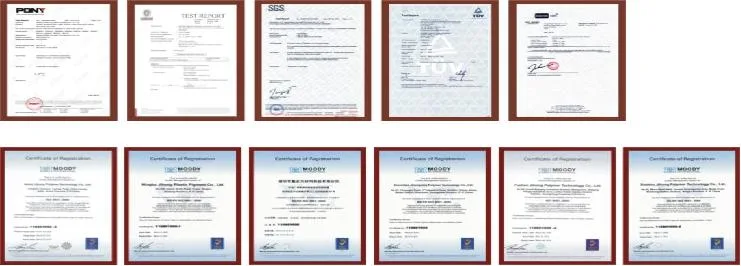
With multiple manufacturing sites in coastal cities in China, CHONGYUAN is specialized in the research and production of color masterbatches and functional masterbatches.The company has a perfect quality management system, cutting-edge production equipment and testing devices, and a sizable technical workforce with years of experience. Our mission is to consistently meet and exceed your needs through our passionate service and reliable quality products. Chongyuan strives to be the best masterbatch supplier in China.
1. Modern production and testing equipment
2. Strong production capacity, high-speed delivery
3. Good quality and competitive price
4. Free sample
5. 24-hour service
1. What are all the type of masterbatch CHONGYUAN manufacturing and selling?
Color Masterbatch: a catalog of 17,500+ color recipes for use in various polymers (including PE, PP, PET, PC, Styrene's, Acrylic, Polyamides etc.).
Functionally Modified Masterbatch (Additive Masterbatch): including Antioxidant, UV, Oxo-Biodegradable, Antislip and Slip, Antiblock, Antistatic, Antimicrobial, Processing Aids, IR, Alcohol Repellent, Blowing Agent, Light Diffuser, Optical Brightener, Fragrance, Chain Extender, Glow in Dark, Clarifying and Nucleating Agents.
Special Effect Modified Masterbatch: including Pearlescent, Metallic, Fluorescent and Fragrance masterbatch...
Mixed Modified Masterbatch: Modified masterbatch with multiple modifiers or additives combined to achieve a variety of performance requirements.
2. What is the advantage of using masterbatch (MB)?
- Low stock holding compared with pre-compounded materials.
- Optimum dispersion of pigments/additives.
- Dust free, no health and safety risks in comparison to undispersed fine powder pigments or additives.
- Elimination of 'trial and error' development or formulation work, as this done by the masterbatch supplier who takes responsibility for color and consistency.
- Reduction in purging/cleaning costs.
- Compared to compounds the masterbatch approach open to variable range of colors and other properties. The alternatives to using masterbatches are buying a fully compounded material (which is more expensive and less open to e.g. color variability of the product), or compounding from raw materials on site (which is prone to issues with achieving full dispersion of the colorants and additives, and prone to preparing more material than what is used for the production run).
- The use of masterbatch allows the factory to keep stock of fewer grades of the polymer, and to buy cheaper natural polymer in bulk.
- The masterbatch can be fairly highly concentrated (in comparison with the target composition), with "let-down ratios"; e.g. one 25 kg bag can be used for a ton of natural polymer. The relatively dilute nature of masterbatch (in comparison with the raw additives) allows higher accuracy in dosing small amounts of expensive components.
- The compact nature of the grains of solid masterbatch eliminates problems with dust, otherwise inherent for fine-grained solid additives. Solid masterbatch are also solvent-free; therefore they tend to have longer shelf life as the solvent won't evaporate over time.
3. How masterbatch is made?
In simple terms, manufacture is a two-stage process: gathering ingredients and then mixing them together by applying heat and shear to produce a homogenized pellet. Generally high or low speed mixers are used to produce a pre-mix of the additives which is then compounded on roller mills, kneaders, single or twin screw extruders. Even distribution (dispersion) and development (breaking down) of the additives throughout the carrier are essential. This processing depends on several key elements: formulation, quality of raw materials, quality of mixing and compounding plant. Finally, the finished masterbatch is pelletized (die-face or strand cut or round).
4. What is most common carrier for masterbatch?
The carrier material of the masterbatch can better to be a specific polymer, identical or compatible with the natural polymer used (polymer-specific). E.g. LDPE, PP, PC, PET, polystyrene can be used for GPPS, ABS, SAN. When a carrier different than the base plastic is used, the carrier material may modify the resulting plastic's properties; where this could be important, the carrier resin has to be specified. The carrier material can be a universal carrier also like wax, EVA etc. However it is better to use a MB which has good compatibility with the customers. Universal masterbatch employs a carrier system that is capable of carrying the high quantities of additives necessary to deliver the end use properties required as well as affording the essential compatibility required across a broad range of polymers.
5. Does the masterbatches influence the property of products?
Some pigments have effect on flame resistance. If used for flame resistace, products should be mentioned as first the detailed applications. Also some additive masterbatch cannot add together in same layers of films since they have adverse effect while using in combination. So in all cases, it is better to consult our technical department for details.
6. Does the masterbatch need to be dried before use?
In general, it can be used directly except for styrenic and polycondensation polymers like PET, PC and some special masterbatch mentioned, which should be dried according to common method and processing condition mentioned in TDS.